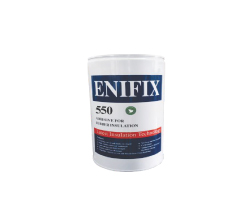
Packing
5 Ltr Tin | 30 Ltr Metal Drum
Enifix 550
(Premium Quality Adhesive for Insulation)
Description
ENIFIX 550 is a premium quality, one component contact adhesive based on polychloroprene rubber. ENIFIX 550 is specially formulated for stress bonding of nitrile rubber & XLPE insulation material. ENIFIX 550 is made from a combination of special resins & additives that produce low odor and provide excellent tack properties along with a very strong bond.
Benefits
ENIFIX 550 has the following features:
- Excellent adhesion and high bonding strength
- Excellent bonding to porous and non-porous surfaces
- Suitable for material under tension
- Usable both indoors and outdoors
- Excellent heat resistance
- Chemical resistant
- Excellent tack
- Low odor
TECHNICAL SPECIFICATION DATA
- Colour : Dark Brown
- Physical form : Liquid
- Specific Gravity (ASTM D 1475-98) : 0.85±0.05 kg/ltr
- Solids Content (ASTM D 1644-01) : 25±2 %
- Viscosity (ASTM D 2196) : 1500-2000 cPs
- Flash Point (ASTM D 92) : < 21C
- Open Time : Approximately : 10-25 Minutes
- Temperature Resistance : Minus 40C to +90C
6 – 7m2/ltr. (Refer to application procedure section)
Application:
Brush, Roller
Shelf Life:
Health & Safety:
- As with all chemicals, caution should always be exercised.
- Consult Material Safety Data Sheet and container label for further information.
Method of Application
ENIFIX 550 is used for air duct insulation, pipe applications, under
deck (metal, concrete) and over deck insulation installation.
ENIFIX 550 is an ideal product for bonding:
- NBR Insulation to GI
- XLPE Insulation to GI
- NBR Insulation to MS Pipe
- XLPE Insulation to MS Pipe
- NBR Insulation in Underdeck
- XLPE Insulation in Underdeck
- Nitrile & EPDM Rubber Insulation
- Closed Cell & PE Cross Link Foam Insulation System
Conforms To :
Free of asbestos, lead and mercury compounds.
Surface Preparation:
Application Procedure:
Note:
The adhesive and the parts to be bonded must be at room temperature for optimum results (do not use below 10°C). The relative humidity must be below 65%to avoid formation of bubbles in the final product. The final bonding strength will depend on the pressure applied. Therefore, press across the entire surface as firmly as possible.